What can I use instead of a cement board?
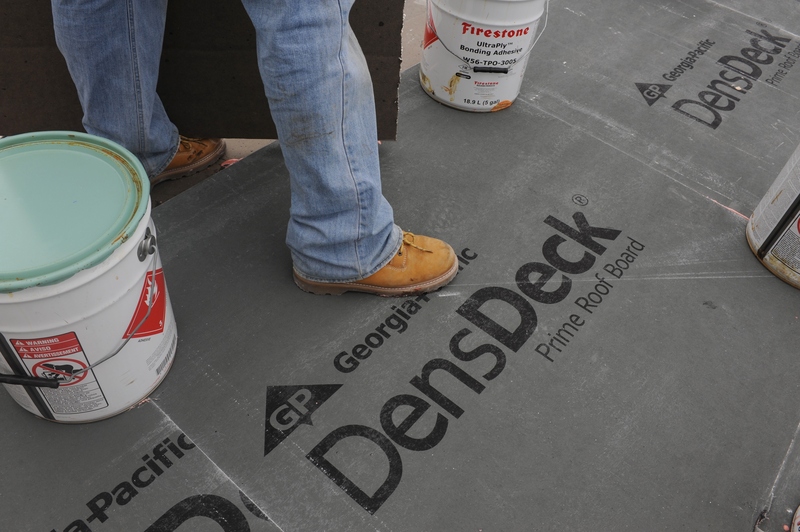
Mat-faced gypsum cover boards are increasingly used as a cement board alternative because they are lighter and easier to install. There are also performance enhancing benefits that mat-faced gypsum cover boards have over traditional cement alternatives.
Cover boards are already considered one of the key components of high performance robust flat roof systems, especially in critical environments. Buildings such as data centres and biotech centres rely on cover boards to increase the roof performance build-up, and minimise the risk of operational downtime. Airports and factories often use cover boards to enhance acoustic attenuation or absorption, in some cases both. Across sectors, cover boards are being increasingly used to bolster the fire resistance of a roof assembly.
To explain why glass mat-faced gypsum cover boards are increasingly replacing the specification of cement boards; comparisons between cement boards and DensDeck® Roof Boards (a mat-faced gypsum cover board) in the following performance areas will be considered:
- Weather protection
- Roof access
- Fire resistance
- Installation benefits
Weather protection for roof build-ups
Overall, cover boards were still relatively underused in the UK in previous years. In contrast, they have been a pivotal part of roof assemblies in Scotland, where the weather is often less favourable. The steady increase in instances of extreme weather and our continued efforts to build better performing buildings resulted in a proliferation of cover boards.
In regard to wind uplift performance, DensDeck® Roof Boards help increase the bond strength with the roofing membrane. This is because the coated mat facer increases compatibility with adhered roof membranes and the cover board itself serves as a robust and homogenous substrate for mechanically fixed membranes. The resulting increased vertical pull through resistance of the roof assembly improves the ability of the roof to withstand wind uplift.
The wind uplift resistance testing data of roof assemblies with cementitious boards, presented by FM Approvals’ RoofNav database, show a performance of up to 270psf (pound per square foot). In comparison, various roof assemblies with DensDeck® Roof Boards have a wind uplift performance up to 285psf for single ply fully adhered on a steel deck.
Most readily available on the market, cementitious boards have the natural ability to absorb moisture. Coated mat-faced gypsum core cover boards are designed to do the opposite and resist moisture absorption. Whilst this does not mean that the boards can be exposed to moisture, the enhanced moisture resistance means they retain their strength for longer should they be exposed to incidental moisture.
Should I choose a cement board or fibreglass gypsum core to protect the roof from foot traffic?
Specification of cover boards can help protect the most expensive part of a roof build-up, the insulation layer, from compression that will negatively impact its thermal performance. As modern commercial buildings feature a large amount of heavy plant and technology on roofs that often require regular, ongoing maintenance, roof traffic can be somewhat frequent.
Both types of cover boards have high compressive strength and can offer robust resistance to foot traffic.
Whilst cement boards are rigid, they can also be brittle and fracture under heavy static loads or frequent foot traffic. Coated mat-faced gypsum cover boards are semi-rigid. They can accept both dynamic and static loads.
Can the fire resistance of mat-faced gypsum cover boards match that of cement boards?
Both gypsum and cement are classed as non-combustible materials as described and tested by ASTM E136. This means both types of cover boards can be used to improve the fire resistance of a roof assembly.
In regard to DensDeck® Roof Boards, the mat facers that can be found on both sides of the board form the first line of resistance to fire. The core of the board is engineered from gypsum. The Gypsum Association says Calcium Sulfate Dihydrate (CaSO4∙2H2O), otherwise known as gypsum consists of 21% chemically combined crystalised water and 79% calcium sulphate. Both natural gypsum and synthetic gypsum share this inherent characteristic. If a fire breaks out, the energy from the heat gradually vapourises the chemically combined water, calcining the gypsum.
DensDeck® Roof Boards are classified as A1 in accordance with EN 13501-1 and non-combustible as described and tested in accordance with ASTM E136 and are included as roof boards in over 180,000 roofing assemblies with a FM Approvals Class 1 fire rating. Our blog ‘How have recent events and legislation affected commercial building envelope specification in relation to fire?’ discussed the fire resistance of cover boards in commercial buildings in closer detail.
Which cover boards are easier to install than cement boards?
There are two main drawbacks of a cement board when it comes to installation and transport. The boards are relatively heavy and require more resources for transportation. They are also harder to manoeuvre on-site and can require specialist equipment to be cut. In comparison, DensDeck® Roof Boards can be cut to size and customised relatively easily in situ using standard tools, and they are easy to install.
As substrates, DensDeck® Roof Boards are compatible with adhered and part-adhered roof membranes and can also be specified with mechanically fastened membranes. Cold, hot and torch applied modified bitumen roofing solutions can be used with DensDeck® Roof Boards, increasing the specification flexibility. Cement boards are less compatible across the board but work well with cold applied bituminous roofing solutions, selected liquid applied membranes, and cold applied bituminous roofing solutions.
Contact us to find out more about the DensDeck® Roof Board range and to discuss how specification of fibreglass mat gypsum cover boards can benefit your project.
Contact Us
Start your project or simply get specification advice by dropping us a message.
One of our team will be in touch as soon as possible.